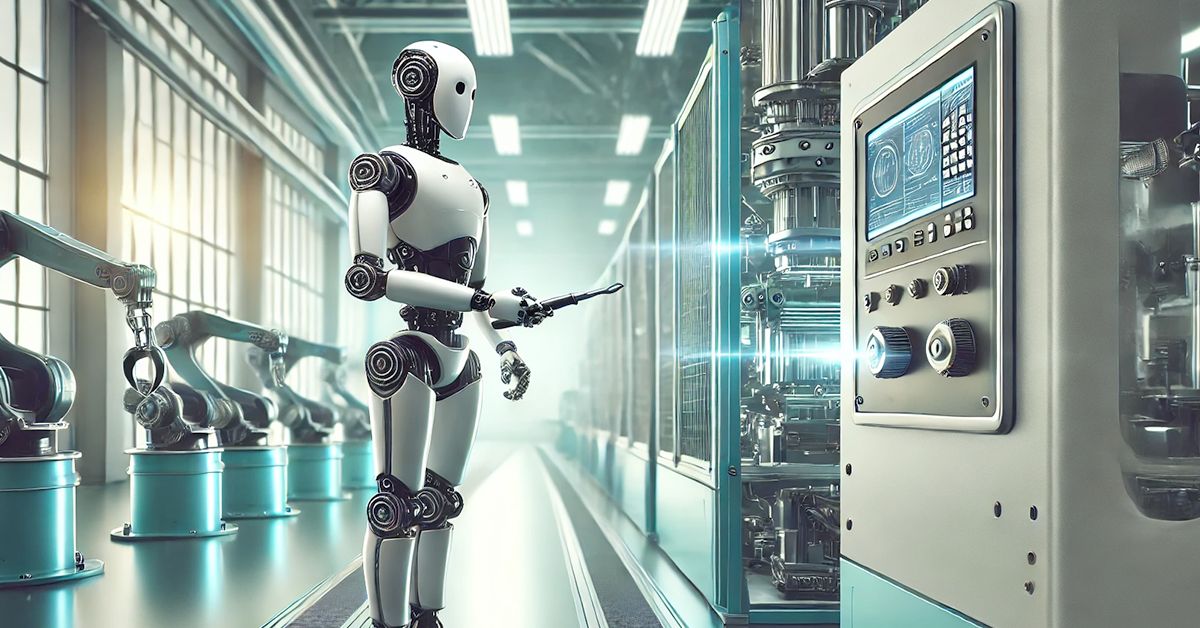
製造業における生産設備の故障は企業にとって避けられない課題です。設備が突如として停止すれば生産ライン全体が影響を受け、顧客への納品遅延が発生する可能性があります。特に重要な設備の修理には時間がかかり、部品の調達に数ヶ月を要するケースもあります。このようなトラブルは企業の収益に直接的なダメージを与えるため、設備の信頼性を確保することが非常に重要です。
INDEX
従来のメンテナンス手法は「事後保全」や「予防保全」が主流でしたが、これらには限界があります。事後保全では設備が実際に故障するまで待つため、突発的な停止による生産ロスが大きくなります。また、予防保全では一定の時間ごとに点検を行いますが、まだ正常に稼働している設備に対して不必要なメンテナンスを行うことが多く、コスト効率の低下を招きます。
こうした中、データ分析やAI技術を活用した「予知保全」が注目されています。これは設備に取り付けたセンサーから収集したデータを用いて故障の予兆を事前に捉え、適切なタイミングでメンテナンスを行う手法です。予知保全の導入によって、突発的なダウンタイムを減らし、設備の稼働率を向上させる事が期待できます。
メンテナンス手法の進化
生産設備のメンテナンス方法は次のような段階を経て進化してきました。
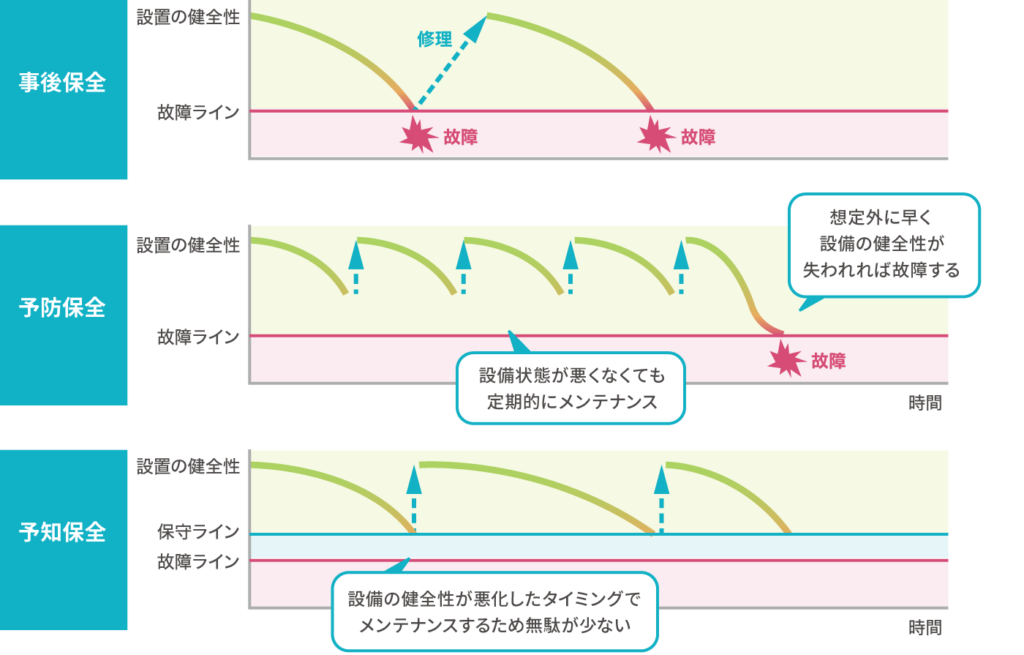
事後保全: 設備が故障した後に修理を行う手法です。ダウンタイムが長くなり、納期遅延やコスト増加につながることが多いため効率的ではありません。
予防保全: 設備が故障する前に定期的なメンテナンスを行う手法です。タイムベースの保全とも呼ばれ、一定期間ごとに設備を点検・修理します。ただし、故障の予兆が無いにも関わらず部品を交換することが多く、過剰メンテナンスによるコストが発生します。
予知保全: AI技術やデータ分析を活用し、設備の異常な兆候を検知して事前にメンテナンスを行う手法です。設備のセンサーから得られるデータをリアルタイムで監視し、異常が発生する前に対応することで無駄のない効率的なメンテナンスが可能となります。
このように設備メンテナンスは単なる修理から予防へ、更にはデータに基づく予知へと進化してきました。特に予知保全は生産性の向上とコスト削減を同時に実現する手法として注目されています。
故障予測
概要
故障予測(または故障予知)は名前の通り、設備が故障する前にその兆候を捉える技術です。生産設備の動作状態を監視し、センサーを使って異常を感知します。例えば、温度の急激な上昇や振動パターンの異常などが検知されればシステムがアラートを発し、故障が発生する前に対応を促します。故障予測技術を活用する事で、予知保全が可能となります。
故障予測のメリット
故障予測システムの導入には多くのメリットがあります。最大のメリットは突発的な故障によるダウンタイムの削減です。これにより企業は生産ラインの稼働率を維持し、納期遅延やコストの増加を防ぐことができます。また、予知保全によりメンテナンスを適切なタイミングで行うことができ、部品の無駄な交換を避けることでメンテナンスコストも削減されます。
さらに、管理者の負担軽減も大きなメリットです。故障が予測できれば夜間や週末に突発的な対応を強いられることが少なくなります。計画的なメンテナンスが可能となるため、従業員の労働負担が軽減され、労働環境の改善にもつながります。また、設備の故障による労働災害のリスクも減少し、現場の安全性が向上します。
AIによる故障予測の仕組み
AIによる故障予測の仕組みはセンサーを用いたデータの収集と機械学習モデルの構築が中心となります。
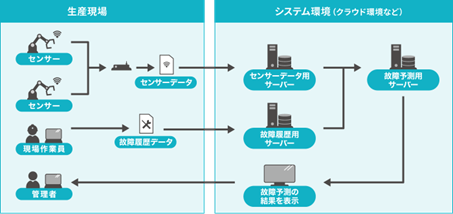
まず生産設備に故障の予兆を捉えるために必要なセンサー(振動、電流値など)が取り付けられ、データが収集されます。これらのセンサーは設備の動作に関する微細な変化を捉えることができ、設備の異常を早期に検出するための基礎データとなります。
次に、収集されたデータはAIモデルの学習に使われます。このとき、故障時のデータなのか、正常時のデータなのか知る必要があるため、センサーデータと故障履歴の突合せを行います。多くの企業では故障履歴をシステムで管理していますが、データの品質はAIモデルの精度に大きく影響するため、正確で網羅的な故障履歴のデータが非常に重要となります。
故障予測システム導入の流れ
STEP1:データ収集の仕組みの構築
故障予測システムを導入するには、まず初めにセンサーを選定し、データ収集の仕組みを構築する必要があります。どのようなセンサーを選ぶかは、予想の精度に大きく影響します。
センサーを選ぶためには、対象となる生産設備の特性を理解することが不可欠です。例えば、モーターを使っている設備であれば電流値や振動データが使われる事が多いです。モーターが異常な動きを始めると、通常よりも高い電流が流れることがあります。また、振動のパターンに変化が生じることで内部の部品が摩耗している可能性を示唆します。
また、設備の動作環境や使用条件を考慮する必要があります。生産現場は過酷な環境であることが多く、温度、湿度、振動などの環境を考慮し、長期間にわたり安定したデータを取得できる耐久性のあるセンサーを選定する必要があります。設置する環境によっては防水・防塵・防爆・耐振動などの対策も必要となります。 センサーデータ以外では、故障履歴が重要なデータとして挙げられます。故障予測システムを構築するためは、正確な故障履歴の記録が不可欠です。例えば、故障が起こった日付だけでなく、正確な時間まで含めることによって、故障直前のセンサーデータと故障直後のセンサーデータを切り分ける事ができます。また、軽微な故障対応や、現場で行った念のために行ったメンテナンス等は記録が残されていない事がありますが、これがデータの品質を低下させ、予測の精度に悪影響を及ぼすことがあります。故障予測に役立つ高品質な故障履歴のデータを蓄積する業務プロセスを策定することが重要です。
STEP2:故障予測のPoC(Proof of Concept:概念実証)
次に収集したデータを元にPoCを行います。
PoCの目的は、AIモデルが現実のデータをもとにどれだけ正確に故障予測を行えるか評価することです。この段階で、システムの効果を事前に検証し、システム構築に進むかどうかを判断します。
まず、PoCでは過去に収集されたセンサーデータを用いてAIモデルを学習させます。これにより、モデルが故障の兆候をどの程度正確に検知できるか検証ができるようになります。具体的には、学習したモデルに対して、学習データにはない期間のデータを入力し、その期間の故障履歴と照らしあわせて予測精度を算出します。
この際に注目すべきポイントは、単に故障を予測できたかどうかだけではなく、「過検知」についての評価も重要です。過検知とは、実際には故障の兆候がないにもかかわらず、AIモデルが誤って異常を検知してしまうケースを指します。過検知が多いと、無駄なメンテナンスが増え、結果としてコストがかさむだけなく、現場の作業者に不必要な負担をかけてしまいます。また、過剰なアラートが頻発すれば、現場の故障予測システムに対する信頼が低下し、最終的に故障予測システムが活用されなくなるリスクがあります。
STEP3:システム構築
故障予測のシステムも、他のシステム開発と同様に「要件定義」、「設計」、「開発」、「テスト」のプロセスで進めます。故障予測システムに限らない話ですが、どのようにこのシステムを活用するのかを明確にする事が重要です。「事前に設備が故障する事が分かったとして、具体的に誰がどのようなアクションを取るのか」を考える事で、システム導入後の運用や必要な機能を整理することができます。
STEP4:運用・モニタリング
システム導入後も継続的なモニタリングが必要です。生産環境が変化するとセンサーから上がってくるデータの特徴が変わる可能性があります。その場合、AIモデルの精度も劣化する可能性があるため、精度を定期的に確認し、必要に応じてAIモデルを再学習させる必要があります。
まとめ
AIによる故障予測は生産現場の効率化と安全性向上に大きく寄与します。しかし、その成功ためは適切なセンサーの選定・設置、十分な量のデータの収集、そしてAIモデルの精度が必要となります。まずはスモールスタートで重要な設備から導入を始め、段階的に範囲を拡大していくことをお勧めします。
これからの生産現場ではAI技術を活用した予知保全がますます普及していくでしょう。そのためには導入時の計画を綿密に立て、現場の環境に適したデータ収集とモデル構築を行うことが重要です。AIを活用した戦略を検討し、次のステップに進むことが企業の競争力を高める鍵となります。
いかがでしたでしょうか。今回はAIで実現する生産設備の故障予測:次世代のメンテナンス手法ご説明しました。今後普及が進むと考えられるAI技術を活用した予知保全について、検討したい、詳細を聞いてみたい等があれば、ぜひお気軽に一度弊社までご相談ください。
関連する記事
・生成AIが変えていくビジネスと世界【前編】
・生成AIが変えていくビジネスと世界【後編】
関連するサービス